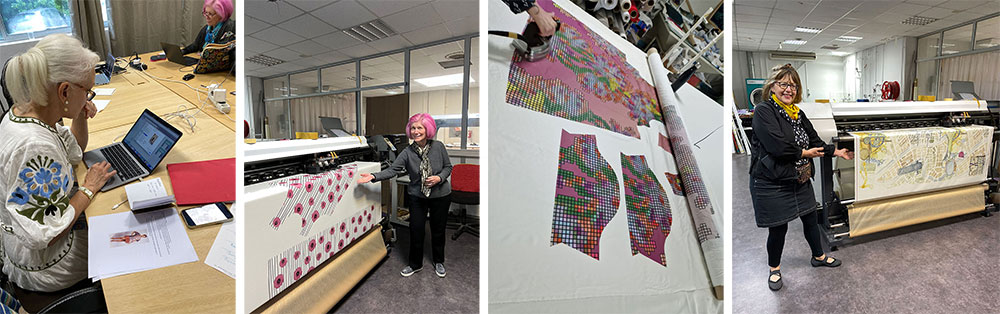
I have just returned after a week of teaching a design workshop hosted by a company in Valsonne, France called Grain de Couleur. This business specializes in digitally printing fabrics for the fashion and textile industry.
Our workshop revolved around two projects:
- Designing what I call an Engineered Design whereby you using a Garment Designer pattern, and marry it with an image, whether it be a photograph or original artwork in Photoshop. This design of pattern/imagery is digitally printed onto natural fibers.
- Designing an overall repeat design fabric developed by creating a motif and setting it up to repeat. This fabric was sublimated onto polyester fabric.
Both processes involved either Photoshop or Photoshop Elements as the tool for combining the print with a pattern or print development in general. Garment Designer was used to create the clothing pattern. We created a full-scale PDF pattern as part of our process.
Our Retreat/Workshop
Four Americans and one Canadian participated in this adventure. We began our workshop in Lyon, exploring the city which has a deep history in textiles (both silk production and jacquard weaving). Various visits to museums/stores/and historical locations were intermixed with workshop time while in Lyon. And of course, there is the food and wine. Lyon is the culinary capital of France so there was no shortage of opportunity to find great cuisine.
After four full days in Lyon, we moved to Valsonne, France to the manufacturing facility of Grain de Couleur. This company is owned by Marie Pierre Dumaine. Marie Pierre is a force in the industry, full of energy and creativity as well as business acumen. I first met her in 2015 when I was on a sabbatical studying Textiles: Past and Future. Since that time, we have developed this collaborative workshop where people from various countries come to France and work in the facility utilizing their resources and talent.
Grain de Couleur’s client list is impressive, and the quality of their work is top notch. They print the fabrics with fiber-reactive dye and then once printed, the fabrics are steamed and washed. It is a time-consuming process, but the results are fabulous. Pascale, the couture seamstress at the company sews the garments for us. Each student cut out their garment and then met with Pascale to discuss the project and the sewing. Pascale doesn’t speak English, but she has become very adept at using a translator on her phone for communication.
Below you can see some of our garments being printed. The beauty of working with Garment Designer patterns in full scale, is that you simply ‘cut out’ the garment, like a cookie cutter.
Each student was responsible for cutting out their own garment.
Student Gallery
Below I will share with you the engineered print garments created by the women in our group. I will save the printed textiles for a future blog.
Addy from Texas
Addy has four grandsons aged 4 and under and they are the focus of her life. She also fosters dogs. So, for her project, she chose to create a hooded cape for her daughter. She built the pattern in Garment Designer.
For her imagery, Addy chose to place the newborn photos of her daughter’s four little boys on clouds. Then, she used the image of her dog to create a border.
Jenny from Louisiana
Jenny chose to create a dress, modeling it after a garment she owned. She created the pattern in Garment Designer and this involved creating two files: the front in two pieces, and the back pattern in one piece.
For her imagery, Jenny’s inspiration was a photo she had taken of ceramic tiles during our time in Burgundy (before the workshop).
She built a motif and a repeating pattern, and planned a border print to use with the garment. Below you can see her finished piece.
Mary, Washington State
Mary is a water colorist and a sketcher. In fact, you could find her out and about daily drawing scenes from our trip. She had decided to make a simple skirt, essentially a rectangle, based on a garment she owned.
Using Photoshop and scanned images of her artwork, Mary built a compilation of her water color images. This was printed on a linen/cotton fabric. Pascale (the seamstress) worked with Mary to create the final skirt as you see below. Mary says that this garment can double as a table cloth!
Look at the amazing detail of Mary’s water color work translated to fabric.
Sylvia, British Columbia
Sylvia saw a garment in a store window in Lyon and decided to use that as her influence for her garment pattern. She built a kimono style jacket as you see below.
For her fabric imagery, she worked with a photo she had of grasses. Using Photoshop, and various filters, she completely reworked the art to an abstract version in blue.
Here is Sylvia in her final jacket.
Suzan, California
Suzan wanted to create an A-line dress and so, she designed this in Garment Designer. She added an extension for a large button at the shoulder which would be a feature of the design.
For her print, she used the image of a poppy she had photographed during our travels. This, she combined with a stripe pattern and laid the imagery into the garment, on the bias.
Here you can see her final garment.
Susan, California
I like to create a project as well, and this year, I wanted to create a dress modeled after a knit dress I own and love. It has a unique box pleat at the underarm on the side seam.
For the imagery, I took some flowers and using Stitch Painter software (our other program), I created a gridded image of the flowers (using the Color Import module to bring in the image, color-reduce it and grid it).
I created a layout of this and positioned it into the pattern shape in Photoshop. This is the layout in the garment.
Here you can see the final garment.
Even though creating these projects was a lot of work, I think I can safely say that everyone had a great time. It was exciting to see one’s ideas turn into reality. Technology over the years has made this possible. And of course, we all love Garment Designer for its role in the process. Thank you to Grain de Couleur for having us on location!
~~ Susan, Creative Director of Cochenille Design Studio